treemuncher
Senior Member
I've recently added a lift axle to the truck that I built as an equipment hauler a couple of years ago. See link https://www.heavyequipmentforums.com/threads/converting-flatbed-to-dozer-ramp-bed.45182/ starting at post #14. I've always been on the edge of my legal limits hauling the Lamtrac and with the plans of hauling the Menzi Muck on this same truck, with tooling, I figured a lift axle and higher gross weights would be a wise investment. I selected a Link 13.5k steerable lift axle (pusher) for my truck with the pre-installed air tanks and controls on the assembly. This pre-installed hardware saved a lot of time and made the installation as painless as possible. As usual, I am a one-man-show and did this by myself without help.
I did purchase a magnetic drill and some 5/8 bits for drilling out the frame. This drill, about $270 on Ebay, was a worthy investment and was worth more than that to me in saved time. It worked like a charm and I never broke the first bit. I selected a mounting location that allowed me to position my brackets on some of the pre-existing holes where the stock brackets were already mounted inside the frame. I removed the required bolts from their positions, clamped the brackets in place and marked the locations with a centering punch.
Once the pre-existing hole locations were transferred over to the new brackets, I drilled out all of the pilot holes on the bracket. With the pilot holes drilled out, and the 2 pre-existing frame hole locations drilled out, the brackets were installed with 2 bolts and clamps to prepare for the magnet drill work. All but 2 holes were cut with the bracket in place. Those 2 holes were marked onto the frame via the pilot holes for centering the drill cutter properly. Once those were cut out, everything fit perfectly.
After the brackets were installed and torqued to specs, I drove the truck's rears onto some large wood blocks to lift the frame high enough to slide the axle assembly under the frame. I used a couple of cargo straps to lift and position the axle so that I could get the bolts started. After centering the axle via the stepped mounting tabs on the mount plates, I was able to torque the axle into place.
The next step was the in-cab controls. Some air lines (provided in the kit) and minor electrical hook ups and the control installation was completed. The one switch lifts or drops the axle and the variable pressure control (locking type) sets the axle down pressure.
Once I mounted the tires on the new aluminum rims and tried the lift, I realized that I had an unforeseen problem - contact of the tires to the bed frame. Fortunately, I over-designed the bed so trimming out the beam was not much of a concern to gain the required clearance. The tire was centered on the beam so trimulation was only required on one beam on each side of the bed.
Results are great. The truck steers better as weight has been removed from the front axle and the truck feels less loaded going down the road. At roughly $210 per rim, I went ahead and added 4 outer rims to the truck to drop the weight and dress it up. Another benefit is that the aluminum rims add spacing between the tires so there is no chance of them rubbing and less chance of picking up a rock.
I did purchase a magnetic drill and some 5/8 bits for drilling out the frame. This drill, about $270 on Ebay, was a worthy investment and was worth more than that to me in saved time. It worked like a charm and I never broke the first bit. I selected a mounting location that allowed me to position my brackets on some of the pre-existing holes where the stock brackets were already mounted inside the frame. I removed the required bolts from their positions, clamped the brackets in place and marked the locations with a centering punch.

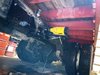
Once the pre-existing hole locations were transferred over to the new brackets, I drilled out all of the pilot holes on the bracket. With the pilot holes drilled out, and the 2 pre-existing frame hole locations drilled out, the brackets were installed with 2 bolts and clamps to prepare for the magnet drill work. All but 2 holes were cut with the bracket in place. Those 2 holes were marked onto the frame via the pilot holes for centering the drill cutter properly. Once those were cut out, everything fit perfectly.

After the brackets were installed and torqued to specs, I drove the truck's rears onto some large wood blocks to lift the frame high enough to slide the axle assembly under the frame. I used a couple of cargo straps to lift and position the axle so that I could get the bolts started. After centering the axle via the stepped mounting tabs on the mount plates, I was able to torque the axle into place.

The next step was the in-cab controls. Some air lines (provided in the kit) and minor electrical hook ups and the control installation was completed. The one switch lifts or drops the axle and the variable pressure control (locking type) sets the axle down pressure.
Once I mounted the tires on the new aluminum rims and tried the lift, I realized that I had an unforeseen problem - contact of the tires to the bed frame. Fortunately, I over-designed the bed so trimming out the beam was not much of a concern to gain the required clearance. The tire was centered on the beam so trimulation was only required on one beam on each side of the bed.
Results are great. The truck steers better as weight has been removed from the front axle and the truck feels less loaded going down the road. At roughly $210 per rim, I went ahead and added 4 outer rims to the truck to drop the weight and dress it up. Another benefit is that the aluminum rims add spacing between the tires so there is no chance of them rubbing and less chance of picking up a rock.