workshoprat92
Senior Member
Well after breaking the second sq100 rear this season I decided to re axle the truck and at the same time get rid of the air bags in favor of hendrickson walking beams. This has been a pretty interesting project so far. Got truck stripped down
donor rear ends. Arvin meritor 20145s
donor hendrickson off of an international. Removing beam end bushings by torching of flanged ends of caps and driving through with jack hammer suspended from the forklift. 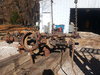
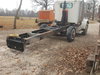
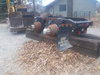

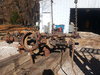