oceanobob
Senior Member
Ran the hammer to break some concrete on recycled pipes that were once embedded, purpose of breaking the concrete was to save the pipes for other uses.
Half hour job, way more fun than a sledge or a pavement breaker.
Upon loading machine on the trailer, noticed the coupler pin was walking out of the dipper. Turns out the securing split pin had sheared. Thinking the loose & worn pin had developed some eccentric loading, I decided to fully investigate and if necessary change the pin and the bushings.
Surprise: The old pin was noticeably worn as were the bushings. 800 hrs on machine.
I had planned for the eventual of this type of situation with a hollow ram set up. For this instance: made a pusher (shoulder bushing) out of cold roll, and got some 1/2" B7 allthread (crmo) w some heavy hex 2H nuts (high pressure pipeliner flange bolt hardware). Out with the pair in one pull at around 6T and the new ones pulled in slightly below flush to allow some room for the seals. The pull in was only one bushing at a time and that was about 1 - 2 ton. Wanted to try it to pull out "as found" just to see if torch was needed to shrink (using principle of flame straightening where heat makes it expand but it also gets weak w temp thus yields that area which leads to change in shape).....could have weld bead but then pusher bush would not fit well LOL
Please note: I intentionally skipped the part of buying the part$.
Trying to keep this thread on a positive note LOL.
Cause the dealer price was $$$.
.
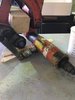
Q: Which direction for the grease seal? Keep grease in, or keep dirt from entering? The as found set up was the latter as best I can discern.
The fitment of the new parts is very nice, minimal play, maybe 5 thou or less. Will do a break-in w moly grease, then shift over to the usual red or blue or the fancy of the day.
L8R
Half hour job, way more fun than a sledge or a pavement breaker.
Upon loading machine on the trailer, noticed the coupler pin was walking out of the dipper. Turns out the securing split pin had sheared. Thinking the loose & worn pin had developed some eccentric loading, I decided to fully investigate and if necessary change the pin and the bushings.
Surprise: The old pin was noticeably worn as were the bushings. 800 hrs on machine.
I had planned for the eventual of this type of situation with a hollow ram set up. For this instance: made a pusher (shoulder bushing) out of cold roll, and got some 1/2" B7 allthread (crmo) w some heavy hex 2H nuts (high pressure pipeliner flange bolt hardware). Out with the pair in one pull at around 6T and the new ones pulled in slightly below flush to allow some room for the seals. The pull in was only one bushing at a time and that was about 1 - 2 ton. Wanted to try it to pull out "as found" just to see if torch was needed to shrink (using principle of flame straightening where heat makes it expand but it also gets weak w temp thus yields that area which leads to change in shape).....could have weld bead but then pusher bush would not fit well LOL
Please note: I intentionally skipped the part of buying the part$.
Trying to keep this thread on a positive note LOL.
Cause the dealer price was $$$.
.

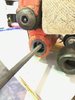

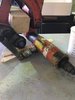
Q: Which direction for the grease seal? Keep grease in, or keep dirt from entering? The as found set up was the latter as best I can discern.
The fitment of the new parts is very nice, minimal play, maybe 5 thou or less. Will do a break-in w moly grease, then shift over to the usual red or blue or the fancy of the day.
L8R