Its all back together! Only thing that I fixed was a squeeky roller... it still drives to the right -_-
I had to put the track back on myself, so I employed the telehandler to hold the track up while I pushed it on with bars and a sledge. It wasn't easy, but took about a solid hour.
I started by chaining the middle of the track to the lift, hoisted it up, pushed it over to the sprocket and lifted the track onto the teeth of the sprocket. I used a ratchet strap through the hole in the sprocket to hold the track; and keep it from falling off and starting over.
Next I pulled on the track by hand to the front of the machine and lowered the track the rest of the way.
I then hooked up a cheap ratchet strap to the bucket and lifted it up onto the front idler wheel. From there I used 2 large 1" square tubes and a sledge hammer to beat the track onto the idler. This is where I spent most of my time.
After It was all on, I put my air jack between the carriage and the track; lifted it up and installed the track carrier roller.
Picked the whole machine up and remove the logs I had holding it up. Let it down and pumped up the track tensioner.
ALSO, on another note, I didnt use the old fan shroud because I figured that it didnt need it... well, pretty much ZERO air flows through the radiator. Ill probably remove it and put this small (but very powerful) motorcycle electric fan on there instead.

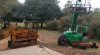
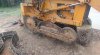
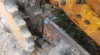
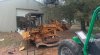