Jason Klassen
Well-Known Member
Hitachi EX120-2 Excavator Service Repair Manual
This is the Highly Thorough manufacturing facility service repair work guidebook for the Hitachi EX120-2 Excavator Service Repair Manual, this Solution Guidebook has actually specificed images as well as action by step instructions
Hey Max, thanks for the link but I already have the manuals for this machine, both in PDF and hardcopy.
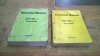
What I really need is info on how much is too much when it comes to wear in the main control valve. I have been reading that a lot of hydraulic systems are designed with 3-8 um (0.00012-0.00031 inch) of clearance between the spool and the bore that it rides in. Seems like once its a little scratched it would be all over in terms of internal leakage.
Does anyone have experience with salvaging control valves? What can and can't be done or when it's too late and time for a new one.