So after getting all the above fixed, I ran the machine hard for about 6 hours yesterday leveling out the ground for my shop foundation. I started to notice I was leaving lots of oil drops on the ground, way more than normal.
I looked underneath, and I could see a steady drip from my right brake housing... Had about an hour before we had to pack up and head home for the week, so I quickly tore into it so I could get parts coming.
It ended up being the seal on shaft between the differential and the brakes.
Unfortunately, I see now that I may have been able to replace that seal without pulling the whole housing. I mangled up the shims and when I pulled the housing I lost almost all the new gear oil I had added after flushing just 2-3 weeks ago.
Question 1: I had used 85-140 gear oil instead of 80-90, figuring I'm not using this in high gear or in the winter, and the thicker oil would be better for the old gears. It is possible that's what blew out the seal?
Question 2: the brake pads got soaked in gear oil. Can I just soak in solvent and burn off with a torch? My ground is pretty flat, I'm not taking this in high gear on the road. I only use the brakes for turning sharp or when it wants to roll slightly when I push the clutch to shift. What can go wrong?
My makeshift shop in the woods is really getting out of hand, so I spent some time organizing tools on pallets. I'm new to all this mechanic stuff, I'm used to using saws and drills and carpentry tools, not wrenches and sockets, etc.
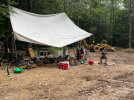